Moduli SPMT da quattro continenti, travi customizzate, slitte ad alta capacità e sincronizzazione ingegneristica. Una campagna di movimentazione eccezionale in ambito minerario, realizzata in tempi record senza smontaggi. Il know-how Mammoet si traduce in precisione strutturale e controllo operativo.
Nel contesto delle grandi operazioni di cava e miniera, quando un impianto entra nella fase di dismissione o rilocalizzazione, le sfide logistiche si trasformano immediatamente in sfide di sollevamento e trasporto pesante. L’intervento condotto da Mammoet per Codelco in Cile rappresenta un esempio compiuto di ingegneria integrata applicata al settore minerario, in cui 16 componenti strategici – inclusi sei elementi primari di un frantumatore – sono stati trasferiti senza disassemblaggio, in un’unica campagna, lungo un tracciato operativo di 4,5 chilometri.
Il cuore dell’operazione ha riguardato due elementi di massa critica: un silo da 1.100 tonnellate e un frantumatore da 1.300 tonnellate, quest’ultimo rimosso e rilocato come singola unità monolitica, senza smontaggi. Una decisione tecnica coraggiosa, ma giustificata da una strategia fondata sulla riduzione dei tempi, sull’abbattimento dei costi e sulla tutela dell’integrità strutturale dei componenti.
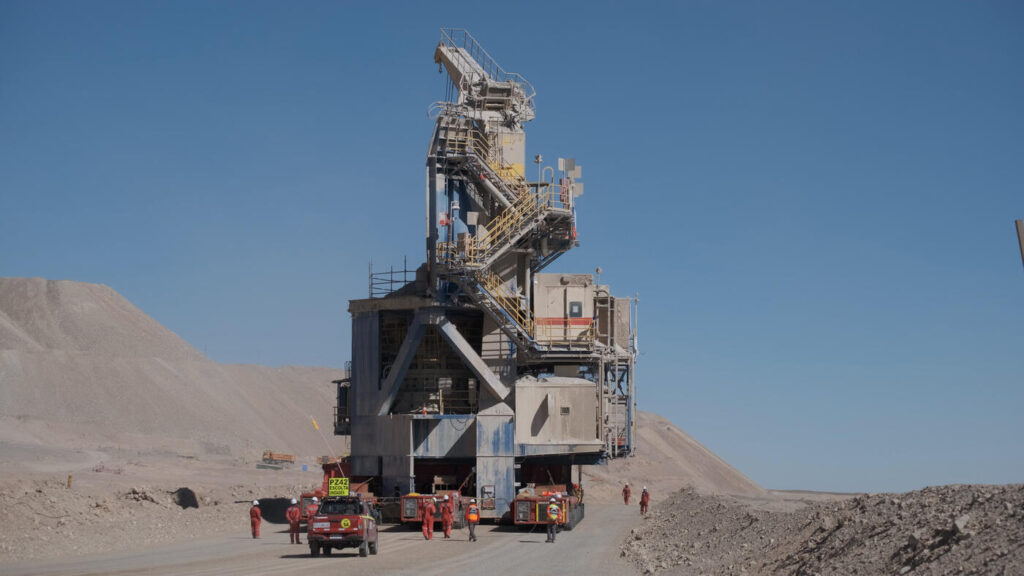
Una pianificazione meticolosa che ha coinvolto le due imprese per un anno e mezzo prima dell’operazione, come spiega Vanessa Labana, Sales Manager di Mammoet: “Abbiamo realizzato i tracciati, i disegni e risposto a tutte le problematiche tecniche, come pendenze, raggi di curvatura e larghezza della sede stradale per garantire il trasporto più rapido possibile”.
Per rendere operativa la strategia, Mammoet ha mobilitato attrezzature e risorse tecniche da diverse sedi internazionali: moduli SPMT sono arrivati dalla Malesia, sistemi di skidding dagli Stati Uniti, strumentazione accessoria dalla Colombia. Il parco mezzi impiegato comprendeva 160 linee d’assi, 8 pattini da 500 tonnellate, 8 sistemi di sollevamento da 400 tonnellate, oltre a travi, binari, martinetti e dispositivi di ancoraggio customizzati.
Ogni componente dei sei principali ha richiesto una metodologia dedicata: in prevalenza, sollevamento tramite martinetti a cremagliera e trasporto su moduli SPMT con travi di supporto. Il sistema di trasmissione ha comportato una sequenza combinata di sollevamento e slittamento laterale di 12 metri, a cui ha fatto seguito la rotazione e il riposizionamento finale.
“È stata una vera sfida – continua Labana – Abbiamo creato una trave di supporto su misura, rinforzata con piastre in piombo nei quattro punti di sollevamento, per evitare deformazioni durante il sollevamento”. Il frantumatore, per massa e complessità, ha imposto un protocollo di estrazione su slitte, innalzamento a quota operativa e successivo caricamento su SPMT, assicurato con sistemi di lashing multipunto per garantire la sicurezza dinamica durante il tragitto. Per consentire l’installazione in configurazione corretta, è stata predisposta una zona rotativa per orientamento a 180° del carico, replicando poi l’intero processo in sito d’arrivo, con abbassamento controllato e posizionamento finale su slitte.
Particolarmente significativa anche la movimentazione dell’unità galleria, su pendenza longitudinale dell’1%: due martinetti idraulici posteriori, azionati in tre fasi, hanno garantito l’assetto orizzontale del carico durante tutto il ciclo di traslazione.
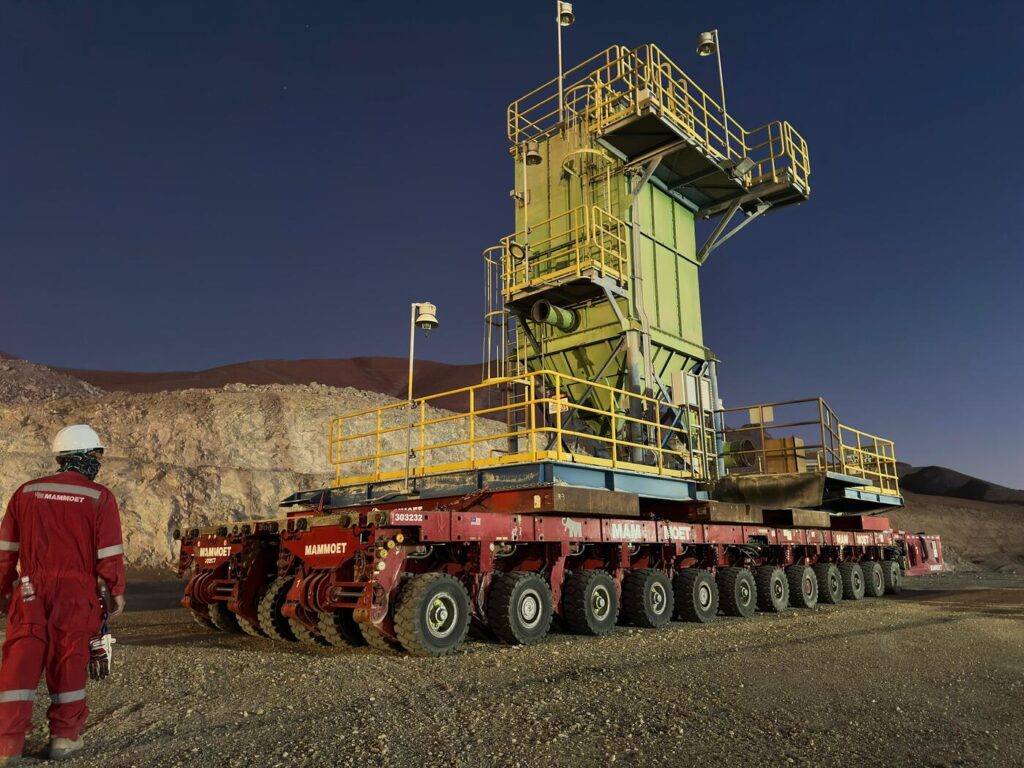
In totale, l’intera operazione è stata completata in poco più di un mese, in anticipo rispetto alla tabella di marcia, evitando smontaggi strutturali e minimizzando l’impatto sulla produttività dell’impianto. Il coordinamento tra team tecnico, logistica, movimentazione e ingegneria ha garantito l’integrità delle attrezzature, il rispetto dei vincoli temporali e la totale sicurezza del personale coinvolto.
“Se avessimo seguito una metodologia tradizionale, Codelco avrebbe dovuto tagliare e smontare completamente le attrezzature, impiegando molto più tempo – conclude Labana – È la prima volta che Codelco affronta un progetto simile. Ora hanno in noi un partner affidabile per i progetti futuri, grazie alla nostra esperienza, flotta e competenza tecnica”.